Cybersecurity Considerations for Industry 4.0
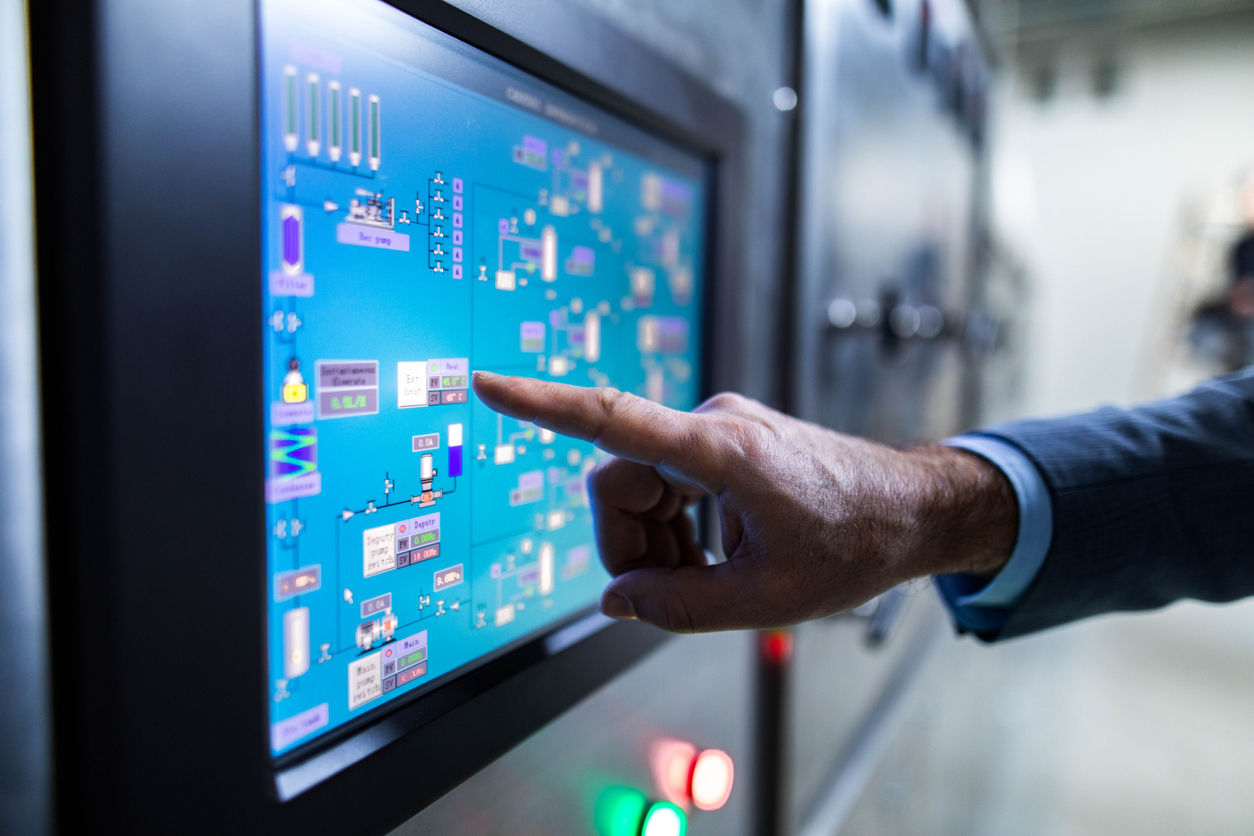

Did you know we are currently in the midst of the most rapid digital transformation in human history? Every day, new and more sophisticated digital technology hits the market. This makes the world easier for businesses and people to operate in them. Welcome to Industry 4.0.
Industry 4.0 is a broad term used to describe emerging technologies utilized by businesses in the modern world. It represents the next phase of digitization in the manufacturing sector. The emergence of Industry 4.0 stems from the increased need for connectivity, business intelligence, human-AI interaction, and data analytics.
Industry 4.0 isn't just about investing in new technology. It's about revolutionizing the way modern businesses live and thrive. The entire manufacturing industry is rapidly changing. To survive in the modern world, business leaders, executives, and owners must accept Industry 4.0 with open arms.
Continue reading to learn more about Industry 4.0, how we got here, and what it means for the future.
The Evolution of Industry: From 1.0 to 4.0
Before diving straight into Industry 4.0, we must understand how manufacturing and technology evolved, where it began, and how it started. There are four distinct periods where rapid technological advancements lead to drastic demographic changes and ultimately helped shape our current world. These include:
Industry 1.0
Industry 1.0 is synonymous with the Industrial Revolution. The Industrial Revolution is commonly referred to as an inflection point in human history. Once industrialization began to take place, humanity changed forever.
The Industrial Revolution began somewhere between the mid-18th century and early-19th century. It began in Great Britain, quickly spreading to Europe, the United States, then the rest of the world. Groundbreaking technology that emerged during this time includes the steam-powered engine, the cotton jenny, and the locomotive engine.
Up until this point in time, most people worked in agriculture. They lived in small communities or farms. However, once the Industrial Revolution began, most of the work began shifting towards factory labor. Likewise, there was a massive increase in urbanization as most factory jobs were in cities.
Industry 2.0
At the beginning of the 20th century, the world entered its second Industrial Revolution. With the advent of electricity in the 1800s and the emergence of steel production, manufacturing and technology accelerated at a level never seen before.
Electricity allowed manufacturers to increase their efficiency and made their factory machinery more mobile. Mass production became commonplace. Industrial magnate Henry Ford popularized the assembly line to boost overall productivity and reduce prices.
Due to mass production, what were once luxury items can now be bought by the masses. For instance, Ford's Model T became the first vehicle the majority of working-class families could purchase.
However, due to rapid industrialization, new and more sophisticated weapons were mass-produced every day. Industrialization during this era helped lift millions out of poverty. But it also led to the two greatest conflicts in human history.
Industry 3.0
Following the destruction of WWII, a third technological revolution slowly began to emerge as nations began to recover. It was at this moment in history that much of our modern technology began to take shape.
During the third Industrial Revolution, manufacturers began producing electronics, such as semiconductors, which ultimately led to the modern computer, smartphone, etc. Likewise, mass telecommunication began to emerge.
As the years progressed, manufacturers put less emphasis on mechanical machinery and more emphasis on digital technology and automation. Not to mention, advancements in telecommunication allowed for fast and effective communication, which enabled globalization.
Industry 4.0
In just the past decade, we have entered a new era of technology. Known as Industry 4.0, it adds to the digital technology transformation we first experienced in Industry 3.0. However, this time around, there is a greater focus on interconnectivity between IoT devices, introducing cyber-physical data, and interpreting real-time data and analytics.
Industry 4.0 provides a much more interconnected, comprehensive, and holistic procedure to manufacturing. It can seamlessly connect digital and physical systems.
Likewise, telecommunication advancements allow for better communication between company departments, third-party providers, and key stakeholders.
Industry 4.0 empowers business owners, managers, and team members alike to make better and more informed decisions and have greater control in their respective departments or roles. They can ultimately leverage these insights to improve business processes, increase productivity, and sustain long-term growth.
Central IIoT Concepts in Industry 4.0
The list of Industrial Internet of Things (IIoT) concepts could go on and on for days. However, there are foundational concepts business leaders should know before deciding to invest in Industry 4.0 technology.
Big Data
Big data may sound like a scary term. However, it's simply large sets of structured or unstructured data. Companies can compile, organize, and store this data. Then, they can use it to analyze market trends, understand patterns, and make informed business decisions.
AI
Artificial Intelligence (AI) refers to the digital technology that mimics the intuitiveness of the human brain. However, it can go far beyond human abilities. Because AI technology is so advanced, it can automate millions of different tasks at an efficiency much greater than humans.
Machine Learning
Machine learning (ML) refers to digital technology that can learn and optimize processes on its own. It does this through AI and does not have to be pre-programmed to complete a specific task or function. The main goal for ML is to have systems that are always optimizing and self-improving.
Real-Time Data Processing
Real-time data processing utilizes AI and ML capabilities to process big data continuously and automatically. By doing so, companies can receive real-time analytics and insights from their structured or unstructured data sets.
Cloud Computing
Unlike traditional computing, where files are delivered to a local server, cloud computing can use different internet servers to host information. On the Cloud, businesses can store, manage, and process information without needing a local network.
M2M Communication
M2M means machine-to-machine. M2M refers to communication between two or more machines through either a wired or wireless network. Through AI and ML, M2M communication is optimized to ensure seamless connectivity and optimal efficiency.
Enterprise Resource Planning
Enterprise resource planning (ERP) are business process management tools that companies can use to better manage information. It can cover broad end-to-end business processes, including HR, finance, supply chain, management, manufacturing, and more.
Ecosystem
Like in the environment, a company ecosystem is a collection of digital systems, technology, and people working homogeneously. All systems work together to push business operations and a company forward. A company ecosystem can include everything from customer development, customer support, financial management, supply chain, inventory, manufacturing, and much more.
Smart Factory
A smart factory is one where a company invests and leverages Industry 4.0 technologies and solutions. Smart factories have Industry 4.0 technology as an integral part of their company's ecosystem and can contain a wide array of solutions.
IoT
IoT is short for the Internet of Things. It is a broad term used to describe all devices in a company's ecosystem connected to the Internet. This can include sensors, software, and physical devices. All IoT devices can be connected to a local network or the Cloud.
IIoT
Like IoT, IIoT, which stands for Industrial Internet of Things. This is a broad term used to describe the connections between internet devices, people, data, and machines as they relate to the industrial and manufacturing industries.
How Do You Know If Your Business Should Invest in Industry 4.0?
It's an honest question many business owners and managers ask. And truth be told, Industry 4.0 may not currently be ideal for some businesses. However, to get a better understanding of whether Industry 4.0 technology would be a great opportunity to add to your current business model, consider the following:
- Do you work in a competitive industry with a lot of tech-dominant competitors
- Do you have difficulty recruiting quality candidates to fill key roles at your company?
- Are you looking to boost profitability and efficiency across your organization?
- Are you looking for comprehensive analytics on a shorter timetable?
- Do you need team members and managers regularly informed with up-to-date news about the company, production, timelines, etc.?
- Are you looking for more integrated business solutions that can span across many departments, such as finance, accounting, customer support, supply chain, manufacturing, and more?
- Do you want to improve the quality of the product?
- Are you in need of digitizing your current business processes?
- Do you need to improve customer satisfaction and customer experience?
- Do you need technology that can deliver fast and accurate insights that helps you make better decisions for your company's future?
If you answered yes to one or more of the questions above, then Industry 4.0 could be an incredibly beneficial investment for your company and its processes. However, if you're still unsure, continue reading to learn more on how businesses utilize Industry 4.0 technology, as well as its benefits, uses, and more.
Industry 4.0 Best Practices for Implementation
Simply incorporating Industry 4.0 in your business and expecting results is not the right mindset. There are some implementation hurdles to overcome. As we gain new wisdom and insight into these implementation challenges each day, we get better at understanding the best practices to get your company Industry 4.0-ready.
To ensure a smooth implementation, consider the following:
Perform an IT Audit
Incorporating Industry 4.0 technology into your business will completely change the nature of your IT ecosystem. However, the audit largely depends on what your current ecosystem looks like. You should audit all the technology you already use, including software and hardware. By doing so, you have a robust understanding of your current digitization efforts, as well as how well-positioned you are for future integration.
Emphasize Connectivity
Although there are plenty of variations on how new technology impacts a business, a core emphasis of Industry 4.0 technology is connectivity. For instance, if you're looking for a way to optimize product production, you should do so in a way that promotes data integration and visibility. When your machinery is working as a collective unit, you can optimize output. However, if your solutions can't integrate nicely, then you've sacrificed connectivity.
Never Neglect Analytics
Another core aspect of Industry 4.0 is the use of advanced analytics. These analytics provide very powerful insights for both your business's current operations as well as future positioning. The more you implement and integrate new technologies, the more data you will produce. Always view this data as an essential asset for your business that you can use to translate into real value.
Understand the Why
One of the best ways to get your team members, executives, and stakeholders on board with Industry 4.0 is for them to understand why you're adopting it. Education and communication are paramount during the implementation process. Your company must work together to understand its current needs and how Industry 4.0 is the solution. Whenever all key personnel is on the same page, you can align your company vision and better set yourself up for long-term success.
Appreciate the Small Wins
Integrating an entirely new system can be time-consuming and nerve-racking. It is best to view Industry 4.0 integration as a marathon and not a sprint. Instead of only looking at the result, appreciate the small wins along the way. If you're always looking ahead, you never get to appreciate the success of the moment. Start small and grow your technology into what you want it to be. And don't rush it!
Benefits from Industry 4.0
Industry 4.0 technology can span the entire product lifecycle and supply chain. This includes everything from design, engineering, testing, quality control, scheduling release, sales, customer reception, and more. Every team member involved in the product lifecycle stays informed through up-to-date news and insights from production and other business processes. Likewise, they receive much more robust analytics.
Here is a quick rundown of some of the benefits of having an Industry 4.0 business model:
Increases Competitiveness
As big-name brands continue to adopt the latest technologies to optimize their supply chain and logistics, you also need to be investing in high-end tech to keep you competitive. These solutions will help you optimize business operations, so you can provide the same level of service as your competitors.
Increases Team Collaboration
Investing in Industry 4.0 solutions can boost team collaboration, increase efficiency, and enable predictive and accurate analytics. This allows team members, managers, and executives to better leverage real-time insights to make better decisions during the day-to-day team interactions.
Attracts a Younger Workforce
The next generation of thinkers and doers are the future of your workforce and your company. To get the best, you must offer the best. Companies that invest in modern and innovative technologies will better position themselves to retain workers of the future.
Reduces Costs and Fuels Growth
With Industry 4.0 technology, you can better manage and optimize all aspects of your supply chain and manufacturing processes. And with access to real-time data insights, you can make smarter and faster decisions that positively impact your business. This ultimately boosts efficiency, profitability, and fuels long-term growth.
Helps You Pinpoint Problems
As with every business, problems naturally arise. However, it is essential to always pinpoint problems quickly and address them before they develop into larger issues. Automation, predictive analytics, and real-time insights can allow your company to be more proactive when it comes to pinpointing and addressing issues as they arise.
Use Cases for Smart Manufacturing
If you are still unsure how Industry 4.0 benefits work, try thinking about how you could apply it to your business. Here are three use cases that can help you better understand how Industry 4.0 technology can provide value for your manufacturing operations:
Predictive Maintenance
Industry 4.0 allows manufacturers to effectively predict when potential problems will arise before they happen. Without IoT technology, preventive maintenance is a manual task. But with IoT systems in place, preventative maintenance is automated and streamlined. Systems are apt at sensing when mechanical problems arise or when machinery needs fixing. Predictive analytics can not only address what has already happened but also proactively prevent problems from occurring.
Supply Chain Optimization
Supply chain is an essential component in manufacturing. With Industry 4.0 solutions, it gives your business better control and visibility over your entire supply chain network. When you better leverage your supply chain management capabilities, your company can outperform competitors by delivering products and services, faster, cheaper, and with higher quality.
Asset Tracking
Industry 4.0 technology allows manufacturers to become more efficient at tracking and monitoring assets during each stage of the supply chain cycle. It helps team members keep a better eye on inventory, quality, and logistics. When factories have IoT systems in place, employees have better visibility of their assets worldwide. Likewise, asset management tasks, such as transfers, disposals, adjustments, and reclassifications can all be optimized and managed in real-time. When reading these use cases, it is best to imagine how you could integrate smart manufacturing technology into your company. From there, you will have a much better understanding of whether Industry 4.0 technology can apply to your business model.
What the Future Holds for Manufacturing
Advancements in technology within the manufacturing sector are nothing new. The industry has been at the forefront of innovation since the emergence of the first Industrial Revolution. However, the advancement in digital technology today pales in comparison to what was available just a few decades ago.
AI, ML, Big Data, IoT, and more are all game-changers that will only become more powerful and ubiquitous in the industry as years progress. Industry leaders looking to reap the most benefits from the new technologies must make data a core asset. Advanced data insights can help deliver better products and customer service. Likewise, they can use these insights to navigate complex business environments to bring about a never-before-seen future.
With the onset of Industry 4.0, the future of smart manufacturing is one where machines can connect and contact each other without the need for human interaction. It will also allow organizations to harness the power of augmented reality, advanced cybersecurity, cloud computing, smart robotics, 3D modeling, and better network coverage through advancements in 5G technology.
Truth be told, we have only just now entered the fourth Industrial Revolution. In the coming years and decades, Industry 4.0 technology is only going to become more advanced. What was once seen as science fiction could become a reality, such as hyper-intelligent AI and completely autonomous business networks.
For anecdotal evidence, just look at the beginning of the 20th century. Many believed flying vehicles were centuries away. Little did they know, the first human-recorded flight would happen in 1903. And by the 1940s, there were thousands of commercial flights every day.
Why You Should Invest in Technology's New Frontier
A new frontier of technology is among us. And now is the time to invest in the future. Industry 4.0 has the potential to revolutionize the manufacturing industry and many others alike. With a greater emphasis on data integration and connectivity, businesses can optimize their workflows and operations, unlike ever before.
And let's not forget. AI and ML are still in their infancy. There's no telling the potential impact those technologies alone will have on shaping our entire future. Just like how the first Industrial Revolution changed our world for the better, Industry 4.0 will change how we think and perceive the world. So, why not be at the forefront of that change?
We understand adopting an entirely new system is a daunting and worrying task. Likewise, Industry 4.0 is still a relatively novel technology. That is why you should partner with a business that will help you take the next step into this new frontier and ensure you have the proper cybersecurity to protect your assets.
At BitLyft, our vision is simple: we believe in building a cybersecurity landscape that protects businesses from all threats. Our team of industry-leading experts will work tirelessly to find solutions that fit your business needs and goals. If you would like to learn more about BitLyft, the solutions we provide, and how Industry 4.0 is shaping the future, feel free to contact us today!